Telemetrics gives studio pedestals the freedom to ‘glide’
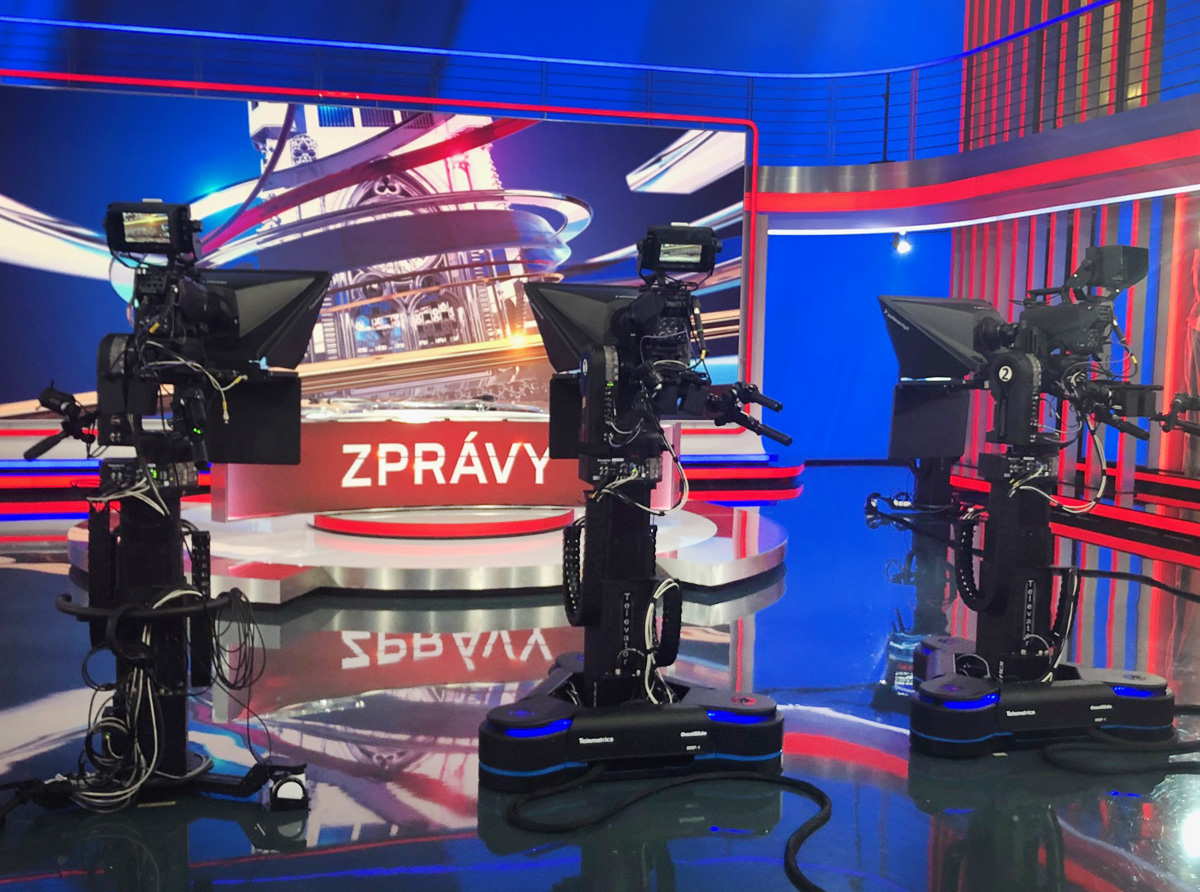
Subscribe to NCS for the latest news, project case studies and product announcements in broadcast technology, creative design and engineering delivered to your inbox.
For Telemetrics, designing and building the next generation of robotic roving camera pedestals meant working, quite literally, from the ground up by rethinking how its OmniGlide rover would move around spaces. In fact, the name “OmniGlide” refers to the way in which the company’s innovative rover can move in any direction without having to make small turns and semi-circles around objects, like other pedestals do.
That makes a huge difference in how the OmniGlide can execute virtually unlimited “crabbing” and other moves to avoid obstacles that are just not possible with other systems on the market. Users have found the innovative design to be an exceptionally smooth and efficient way for the rover to move on air.
“The OmniGlide does not use wheels but runs on spheres,” explained Michael Cuomo, vice president at Telemetrics, who is the third generation of his family to create robotic camera control products for the broadcast industry.
Because OmniGlide was designed and engineered from scratch, it uses the most compact components possible, including ones custom built in Telemetrics’ Allendale, New Jersey headquarters to fit within its low profile. Despite this, the rover can safely support full sized teleprompters, feedback monitors, viewfinders and other gear without tipping over.
When robotics are operational, OmniGlide knows its position down to a few millimeters without ever needing to be re-homed, re-positioned or re-calibrated beyond the initial deployment. Instead, a small camera on one corner of the base uses the reflection off a series of stickers in the studio ceiling or grid.
“Fusing the data that comes in from the optical system with the internal servo allows us to get really smooth, accurate motion,” Cuomo said.
All three corners of the rover have their own independent optimized drive systems, but also communicate with each other thousands of times per minute for incredibly accurate and fine-tuned absolute positioning.
OmniGlide has a virtualized view of the studio, called “Studio View” that shows real-time data about every camera, including each camera’s current position, elevation, pointing angle, pan angle and zoom setting. The view is integrated with models of the set and structural elements of the space so it replaces and builds upon the traditional spy cams that crews use to track camera positioning.
OmniGlide also has a unique take on manual control.
At first glance, the peds look like they’re equipped with a traditional pan bar — but, like everything Telemetrics sells, it’s been engineered with carefully thought out features. It includes thumb controls inspired by video game controllers to make it easy and intuitive to manually control a camera, providing production teams with the ultimate flexibility to change or adjust shots on the fly.
Cuomo explains that OmniGlide isn’t necessarily meant to replace camera operators — but rather to augment them. A human can instantly grab the pedestal’s pan Cobotic bars and take over control without even flipping a switch, bringing unparalleled flexibility for productions that might need to change course unexpectedly.
OmniGlide integrates with major studio production automation systems, including Ignite, ELC and Vizrt Mozart, with plans to enhance the user interface expected soon. The EVS Cerebrum Broadcast Control System is also supported.
Used in combination with the Telemetrics RCCP-2A Robotic Camera Control Panel, the OmniGlide can ensure talent is always centered in the frame, even when they are shifting in their seats, by leveraging Telemetrics’ exclusive reFrame™ Automatic Shot Correction software. It utilizes three different layers of talent tracking that ensures a successful production every time, explained Cuomo.
Available on the OmniGlide as well as other Telemetrics robotic camera control products, reFrame combines facial tracking, object tracking and ultra-wideband sensor layers that can work together to intelligently monitor on screen action and make adjustments immediately. Add in an artificial intelligence wrapper and the system has become the most reliable on the market.
OmniGlide also features automatic zoom framing for when a subject walks toward or away from a camera, a need that’s more common in the live event space. The ultra-wideband tracking layer is also more frequently used with live events, but is useful in any application where a person or talent being tracked might lose direct line of sight with the camera, such as having a speaker or host walk into an audience.
Combined, all of these features give OmniGlide the ability to do complex on air moves for everything from the top of a newscast, bumps or the increasingly popular use of video walls to enhance storytelling.
“We wanted to bring jib-like shots to a rover,” said Cuomo, noting that Telemetrics offers multiple column options for OmniGlide units depending on the height a production wants to be able to achieve— among other factors.
Unlike most jibs or handheld camera rigs, however, OmniGlide can support a full sized teleprompter for talent while also being safer to operate in studios that are increasingly stocked with tens of thousands of dollars’ worth of LED panels that a jib can easily ram into.
Crew safety is always an issue with studio robotics, so Telemetrics has added multiple safety features to OmniGlide that can not only stop a rover if needed but it can also prevent accidents before they happen. The motorized base is outfitted with three sensors that track any nearby objects — whether they be people, set walls or movable set pieces. These sensors not only know something is nearby, but also how far it is from the unit, thanks to millimeter level position awareness. In this way it intelligently “learns” the space in which it is operating and makes adjustments to its movements accordingly and in a fully automatic way. Each corner will flash orange, based on which side is detecting a possible obstacle—giving talent and crew relevant and actionable information—and turns blue when all is good.
That’s an upgrade over the bumper systems many robotic peds rely on to detect if they’ve hit something.
“This easily can prevent a pedestal from causing thousands of dollars in damage to video walls,” explained Cuomo, as well as proactively working to prevent human mishaps.
OmniGlide also recently added a “Path Planning” feature that lets pedestals move from Point A to Point B, intelligently navigating around anchor desks and other set pieces that are in the middle of a studio space without having to engage the onboard sensors to avoid the obstacle each time.
Operating or “Go” zones, meanwhile, can be established to designate unrestricted areas of the studio, ensuring the rover can easily handle on-air moves without interruption (collision). This comes in handy, for example, with sets boasting portable video panels or walls that the base sensors can’t detect there’s no underlying structural elements near the floor.
Because of their slimmed down hardware manifests, Telemetrics was able to make OmniGlide bases extremely sleek and streamlined.
“We’ve had clients say the rovers become part of their set,” said Cuomo with a laugh, explaining that wide bump shots showing the units look great on-air thanks to the LED indicators in the bases.
Besides looking cool on camera, these indicators actually do serve practical purposes such as letting talent and crew know where a rover is even if it’s cloaked in darkness or they are facing glare from lighting.
Because Telemetrics designs and builds everything in house in its Allendale factory, it’s able to maintain tight control over quality. It avoids using easily cracked plastics in favor of industrial metal housings with a focus on creating robust gear that’s meant to be used daily in demanding environments.
Telemetrics also has built in numerous diagnostic sensors and tools across its product lines that it can use to troubleshoot and even prevent mechanical issues remotely. This remote diagnostic capability came in handy during the worst of the pandemic.
While the company offers multiple off the shelf options with traditional model numbers, it can also custom build solutions for broadcast, corporate, educational, house of worship, surveillance or medical applications. It has designed and engineered solutions for NASA, MLB, NBA Google, Apple and numerous other companies and organizations large and small.
“We’re a proud engineering focused company, not a box sale company,” said Cuomo, who says he still loves diving into code or problem solving with product engineering and design.
Learn more about Telemetrics and its broadcast expertise on its website.
The above column is sponsor-generated content from Telemetrics. To learn more about sponsor-generated content, click here.
Subscribe to NCS for the latest news, project case studies and product announcements in broadcast technology, creative design and engineering delivered to your inbox.
tags
Robotic Camera Control, robotic cameras, Telemetrics, Telemetrics OmniGlide, Telemetrics OmniGlide Roving Platform
categories
Partner Content