Industry Insights: Cloud-based production reshapes switcher capabilities
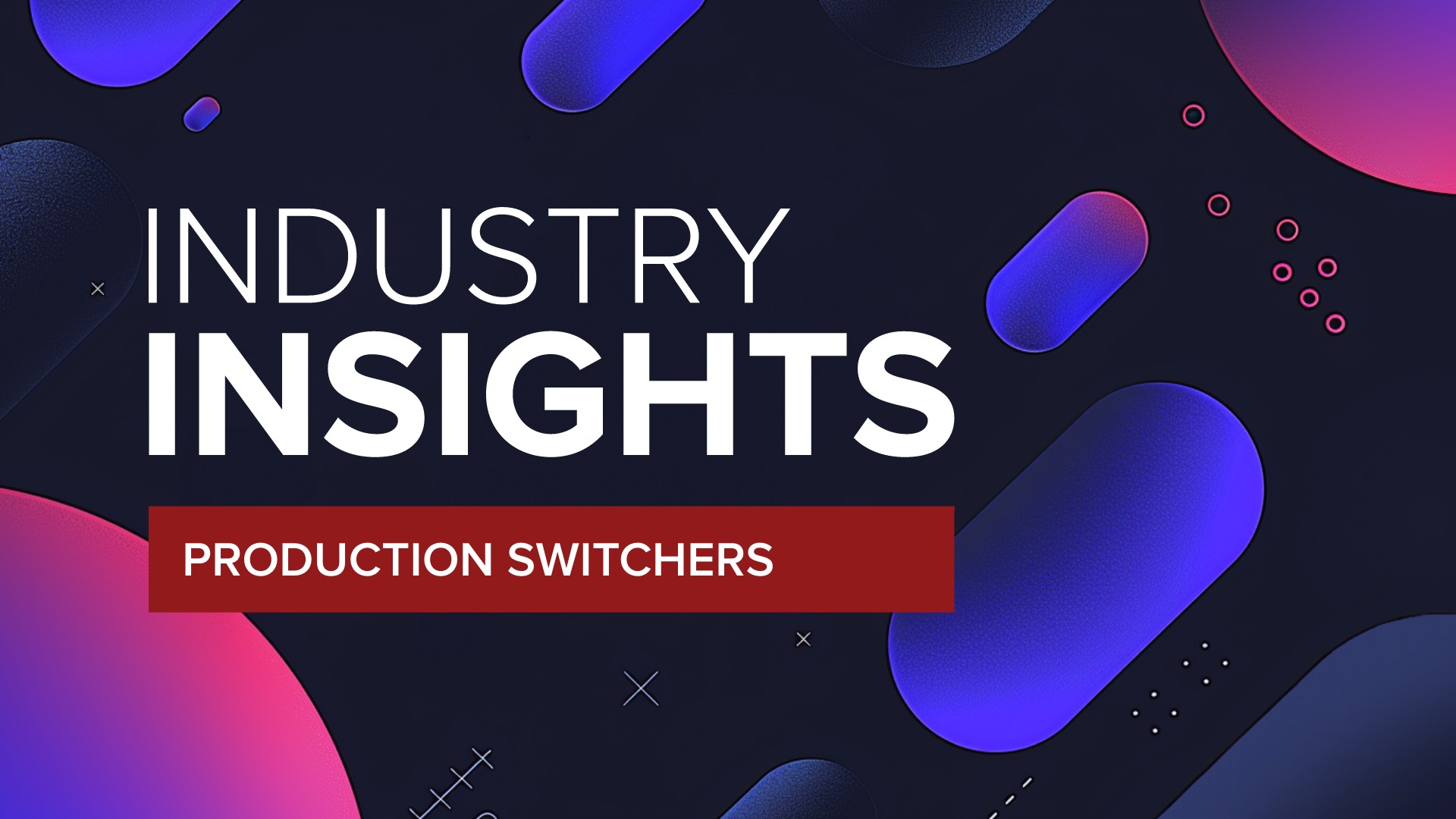
Subscribe to NCS for the latest news, project case studies and product announcements in broadcast technology, creative design and engineering delivered to your inbox.
This edition of our Industry Insights series delves into the evolving landscape of production switchers, bringing together industry experts to discuss how new technologies are primed to reshape workflows.
From the rise of IP-based production to the role of touch panels and enhanced resolutions, production switchers (or vision mixers) are undergoing significant changes.
Vendors share their insights on how switchers are adapting to support remote workflows, cloud-based production and the increasing demand for flexibility and scalability in live production environments. The roundtable highlights current trends and emerging technologies influencing next-generation switchers, offering valuable perspectives on the future of production switching.
Key takeaways from the Industry Insights roundtable
- IP-based production has removed geographical barriers, allowing switchers to be operated from any location, enhancing scalability and flexibility.
- Touch panels and new interfaces offer simplified, customizable control solutions, making switchers easier to operate, especially for non-technical staff.
- Enhanced resolutions and new formats require switchers to handle more complex video signals while maintaining performance and output consistency.
- Software-based switchers provide greater flexibility for remote productions, although hardware switchers still offer superior reliability and lower latency.
- Advancements in remote production workflows enable switchers to support various video-over-IP protocols and allow full remote operation, streamlining production.
How is IP-based production changing workflows with regards to switchers?
Deon LeCointe, director of networked solutions, Sony Electronics: IP-based technologies within production are enabling media organizations to scale their live production environments in ways that had been particularly challenging to implement in the past. For example, by removing the geographical barriers that have traditionally existed between production resources (i.e., production switchers) and production personnel, operators can now connect to and operate equipment regardless of their location across enterprise. This level of connectivity has ushered in a new era of production which can occur at virtually any scale from practically any location.
Keith Vidger, principal technical consultant, Panasonic Connect: Switchers that support IP standards like SMPTE ST 2110 can connect to a far greater number of sources compared to traditional SDI router/switcher infrastructures. ST 2110 also supports redundancy and PTP, which enables signals throughout the production process, that acquire different amounts of latency, to be timed automatically before transmission. One of the biggest workflow improvement enjoyed by IP-based production is the advent of Smart Routing, which allows the switcher to automatically and dynamically subscribe to a vast network of ST 2110 streams.
Ryan Hansberger, head of product development for video mixing, Vizrt: IP-based production simplifies and streamlines workflows by making any networked video source instantly accessible to the switcher, eliminating the need for extra cabling or workflow adjustments. This approach maximizes flexibility, allowing for seamless, on-the-fly changes to content and sources.
Satoshi Kanemura, president, For-A Americas: IP technology makes possible three critical areas in live production: remote production; software defined architecture provides agility and customization; and lastly a completely cloud-based workflow enables the ultimate in flexibility and keeps cost down.
Greg Huttie, VP, production switchers, Grass Valley: IP’s impact on broadcast switchers and remote productions has been huge. The ability to input and output sources bidirectionally utilizing fewer cables with minimal delays for ultra-low latency is critical in any live production set-up. Resources can now be easily scaled whether they are uncompressed or compressed, HD or UHD 4K, FPGA or GPU processed.
How are touch panels and new control interfaces changing switchers?
Keith Vidger: Switcher touch panels are ideal for those who work on a production but require ease of use, such as producers or volunteers who may be intimidated by the complexities of traditional control panels. Touch panel solutions usually consist of software and a touchscreen monitor and are far less expensive than traditional switcher control panels. The design of a touch panel, which combines a multi-viewer output from the switcher with basic source selection and macro recall, offers an all-in-one control solution that can even be operated remotely.
Nigel Spratling, VP, production switchers and video servers, Ross Video: Modern productions are increasingly demanding, requiring reliable and intuitive control solutions. Interactive touch panels and new control interfaces offer operators more confident control under pressure. These panels can be customized for different applications, such as switching aux outputs, triggering macros, or setting up additional soft panels on computer screens for remote or local operation.
Satoshi Kanemura: Gen Z grew up with touch panels and are not familiar with hard panels at all. Still, certain functions still require hardware control. Aside from that, touch panel operation has increased dramatically in popularity. Web GUI’s are used a great deal for remote control of switchers.
How do enhanced resolutions and production formats impact switcher design and capabilities?
Ryan Hansberger: Enhanced resolutions and new formats demand switchers that can handle larger or more compressed video signals without sacrificing throughput. Software-based switchers are uniquely positioned to adapt quickly to these changes, leveraging advances in general computing hardware to maintain performance and source count.
Nigel Spratling: The increasing variety of video formats, including different sync and non-sync signals, as well as color spaces like SDR and HDR, requires modern video switchers to be more versatile. Switchers must now incorporate functionalities such as frame synchronization, color correction, HDR conversion, and format conversion (e.g., HD to UHD). These enhancements ensure that switchers can manage a broader range of inputs and deliver a unified output, meeting the demands of today’s more complex production environments.
Greg Huttie: The higher resolution formats demand much larger signal bandwidth as required to handle UHD 4K 2160p signals that the production switcher must process to maintain a consistent I/O footprint and functionality regardless of format. Additionally, customers desire to mix both Standard Dynamic Range (SDR) with High Dynamic Range (HDR) signals or provide program feeds in both adds a request for inclusion within the switcher.
What features in modern production switchers are enhancing multi-camera live streaming capabilities?
Kelli Matthews, marketing manager, JVC Professional Video: Many video switchers come with a variety of video effects that can be implemented for all types of productions. Among these are the ability to integrate with virtual sets or to deploy graphics directly into the stream.
Satoshi Kanemura: ISO recording and timeline editing with real time encoding.
How do software-based production switchers compare to hardware solutions in terms of reliability and performance?
Deon LeCointe: Over the last few years, we have seen amazing advancements in the realm of virtualized production switchers which can run on Commercially of the Shelf (COTS) hardware. While these software-based offerings can complement a hardware-based production switcher for producing alternative feeds or sub-shows, they still lack the horsepower of today’s purpose-built production switchers. However, it is just a matter of time until we see software-based solutions that provide the same specs as their hardware-based predecessors.
Ryan Hansberger: Because technology is rapidly changing, the essential difference is that hardware solutions lock you in with the capabilities of today, while software-based solutions provide you with much easier deployment when new advancements are made. A competent software-based solution lets users upgrade to the new advances with a simple update or software installation. Software-based solutions also provide greater flexibility for remote productions, enabling them to happen essentially anywhere, while maintaining reliability and performance.
Satoshi Kanemura: Software-based switchers have more flexibility, expandability, and agility than physical switchers. A hardware switcher’s latency for processing and operation is minimal, and there are no potential network security issues.
Greg Huttie: Both software-based and hardware-based production switchers can be optimized for reliability and performance across various applications. Key features such as redundant IP networks, handling multiple formats, and power supplies can enhance the reliability and performance of both types of switchers. The choice between software and hardware solutions often depends on specific production needs rather than inherent limitations in reliability or performance.
What advancements have been made in production switchers to support remote production workflows?
Deon LeCointe: The advent of advanced Media over IP technologies including SMPTE ST 2110, SRT, and NDI have ushered in a new age of connectivity for production switchers which has enabled new remote workflows. Similarly, the ability to virtualize a production switcher which can be run on premises or in the cloud has given media organizations incredible capabilities to produce shows of varying sizes and deploy resources, on-demand, to where they are most needed.
Keith Vidger: Remote production typically starts with a switcher’s native ability to input compressed streaming sources such as SRT. The more high-quality streaming inputs a switcher has, the higher the production value. Operation of an on-prem switcher can happen remotely as well, if the switcher supports streaming of its multi-viewer outputs and can connect control panels to the switcher via the internet.
Edgar Shane, general manager of engineering and project development, JVC Professional Video: When shopping for cameras and video switchers, look for those with HEVC and NDI/SRT support, which allows you to send HD, 4K, H.264 and HEVC (or I-Frame) over the same Ethernet connection. Some devices can simultaneously output NDI and SRT for local NDI switching or monitoring and remote production over the internet (REMI). The integration of NDI and SRT into JVC’s video mixers makes it possible for customers to have a simple and cost-efficient workflow and ensures interoperability with many other brands of production equipment.
Ryan Hansberger: Production switchers now support a broader range of video-over-IP protocols and enable full remote control, benefiting from advances in remote desktop and KVM software. These enhancements, combined with improved cloud connectivity, make remote production more seamless than ever.
Nigel Spratling: To support remote production workflows, switchers now offer various operating modes that enable remote control and operation. Control panels, once tethered to local processing frames, can now be located remotely and connected via VPN technology. Additionally, comprehensive software-based control panels allow operators to manage productions from virtually anywhere.
Greg Huttie: There are a variety of solutions to enable remote productions, for example, the switcher control panels can be connected to the hardware processors via wide area IP networks, IP video signals can be distributed to the processors via IP infrastructures, the integration of JPEG XS significantly reducing the required bandwidth, and with software-based production switchers, the location of the signal processing can be selected between on-premises or the cloud.
What features are you implementing to future-proof your products?
Deon LeCointe: Sony’s approach to live production focuses on hybrid processing and operations which allows media organizations to combine the power and reliability of on-premises with the flexibility of the Cloud. This keeps mission-critical processing on-premises while using the scale and cost-efficiency of Cloud services to gives content creators immense flexibility to scale their production environments with their needs. With this in mind, Sony has introduced the MLS-X1, a scalable live production switcher platform that can grow or shrink based on the demands of the show, and the M2L-X, a software-based live production platform that can run on premises or in the cloud.
Keith Vidger: Panasonic Connect utilizes future-proofed technology such as ST 2110 for connectivity to uncompressed sources in traditional resolutions from 720P to UHD, and soon IPMX for non-traditional resolutions which can be used without synchronization. To enable redundant operation, control with third-party panels, and even browser control over Wi-Fi, Kairos uses REST API. Kairos also uses the popular LUA format for its macros, which employs intuitive scripting for powerful functionality, such as triggering actions based on tally state.
Kelli Matthews: JVC’s switchers, such as the new KM-IP12S8PRO vMix switcher, have an open box system, which allows users to add additional items as their needs and budget grows. Powered by vMix Pro, this switcher is ideal for large-scale productions of live sports and events in facilities with multiple cameras and video sources. The switcher can be scaled up to eight channels of instant replay and supports 50+ inputs for live camera production, including four 3G-SDI and up to eight 1080 60p NDI.
Nigel Spratling: Future-proofing our products involves several strategies, including regular software updates that deliver bug fixes and new functionalities. We also offer optional features that can be activated as needed through efficient software licensing. This approach ensures that our products adapt to evolving technological trends and user requirements, providing long-term value and performance.
Greg Huttie: We continually listen to users input and their continual increased production requirements. The overall modular structure of the hardware-based K-Frame’s I/O and processing boards affords either introduction of new boards or adding functionality (some examples: introducing onboard JPEG XS signals processing, color mapping of HDR and SDR, and adding additional clean-feeds). With the software-based switchers, extension of functionalities is possible at any time without changing specific hardware and is always therefore future-proof.
Satoshi Kanemura: We’re implementing software-based architecture that easily supports any future requirements, all formats, and all compression standards.
How are production switchers evolving to support cloud-based production environments?
Deon LeCointe: We have already seen the introduction of software-based production switcher platforms, like Sony’s M2L-X, which can be deployed on premises in COTS hardware and on the Cloud. The current phase in the evolution of production switchers will focus on virtualizing traditional switcher functionality into software platforms. The next evolution will be migrating that same functionality to the cloud and increasing the performance to match hardware-based platforms.
Ryan Hansberger: Production switchers are continuously evolving through optimizations and expanded support for various system architectures to meet the demands of cloud-based environments. Collaboration with cloud providers during new infrastructure deployments ensures that switchers remain at the forefront of cloud production advancements. But it’s not just the switchers themselves that are evolving; new tools have been developed to make cloud adoption even easier.
Satoshi Kanemura: Cloud-based switchers expand the particular market for live production to those such as remote production and streaming-based businesses who in the past could not afford the capital expenditure of an on-premise, physical switcher.
Greg Huttie: The software-based production switchers already support cloud processing in addition to on-premises processing on COTS servers. The location of the processing does not limit the functionality or performance of the production switcher and can therefore be freely selected as required.
What emerging technologies are likely to influence the next generation of production switchers?
Keith Vidger: The architecture of traditional switchers hasn’t really changed in 70 years, with a fixed number of M/E’s, keyers, transitions generators, etc. The future of production switchers will be based on GPU technology for all image processing, with no fixed limits, enabling higher production value, easier operation, and creative freedom. GPU processing enables layer-based operation, layout-free multi-viewers, image conversion on all I/O, mixed-format media playback, and Canvas scene output capability that’s 32 times larger than a full HD M/E, at a lower cost than conventional switchers.
Ryan Hansberger: Artificial intelligence is poised to revolutionize software switchers by enabling new AI-driven features and optimizing existing workflows. From AI-powered super resolution to automated production tasks, AI will play a critical role in the future of switching and software-based solutions are well positioned to take advantage of the technology.
Subscribe to NCS for the latest news, project case studies and product announcements in broadcast technology, creative design and engineering delivered to your inbox.
tags
Deon LeCointe, Edgar Shane, FOR-A, Grass Valley, Greg Huttie, JVC, Keith Vidger, Kelli Matthews, panasonic, Panasonic Connect, Ross Video, Ryan Hansberger, Satoshi Kanemura, Sony, Vizrt
categories
Heroes, Industry Insights, Production Switchers, Voices