Important considerations when selecting LED display technology for broadcast studios
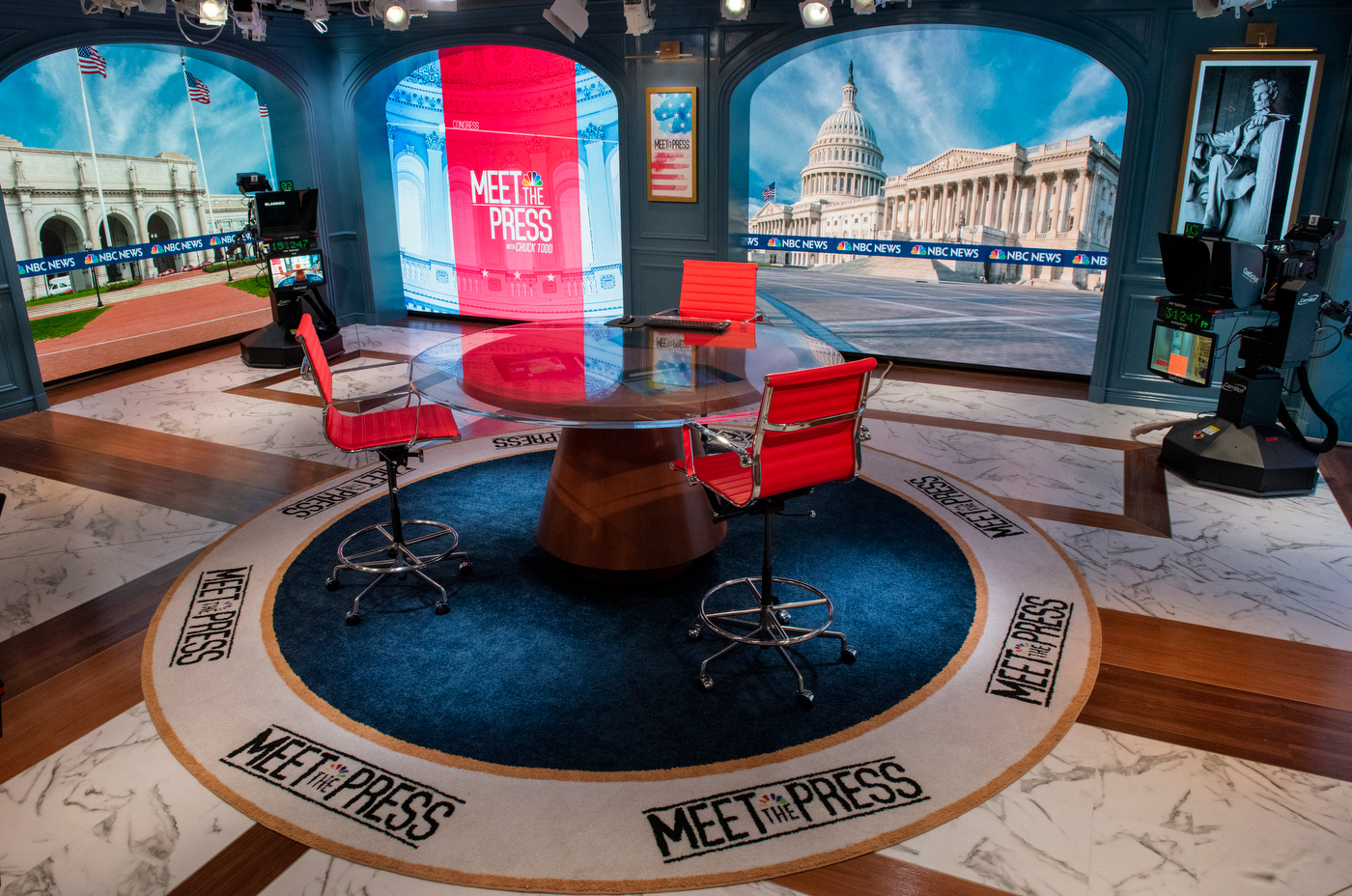
Subscribe to NCS for the latest news, project case studies and product announcements in broadcast technology, creative design and engineering delivered to your inbox.
LED video walls have become must-haves in TV studios — and it’s easy to focus solely on the stunning picture that these installations deliver while overlooking the nuts and bolts (or, in this case, diodes and SMDs) of the technology behind it all.
“One of our core values is to instruct and educate customers as much as possible during the buying process,” said Aaron Kipfer, the chief technology officer at Neoti, a company that develops, designs and manufactures its own LED panels for a wide variety of applications.
That starts with truly digging into what the video wall installation will be used for, how it will be viewed and shot, and a myriad of other important factors.
Pixel pitch matters when selecting studio display technology
Most broadcast applications focus on providing high-quality backdrops behind talent, which typically requires higher resolution LED panels, so Neoti typically recommends panels in the 1.2 to 1.8-millimeter pixel pitch range.
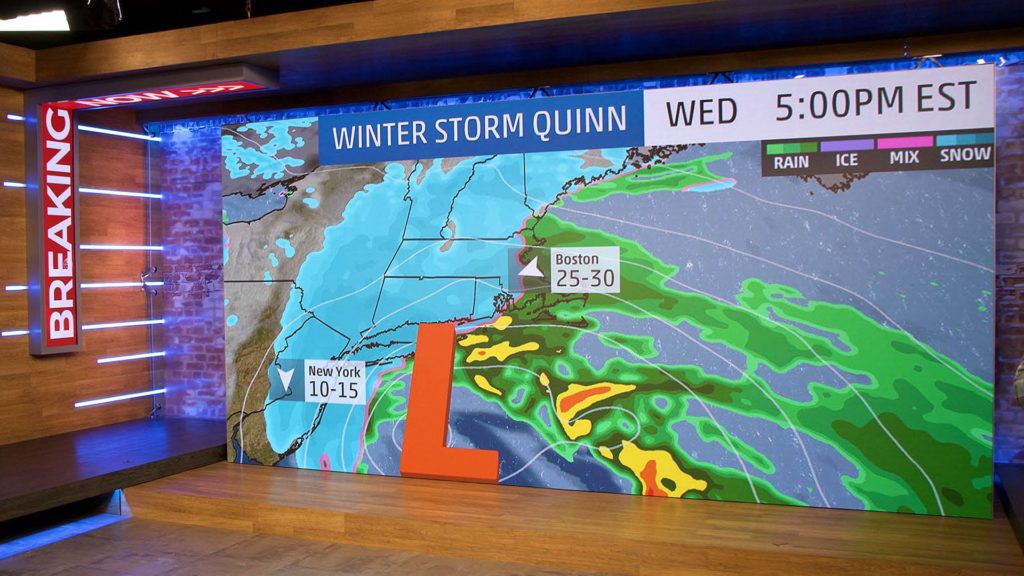
LED video wall at The Weather Channel from Neoti.
However, the set design industry has also been exploring layered or diffused backgrounds that can use lower resolution panels — even up to 20 millimeters.
Thinking outside the rectangle
Another big trend that Neoti is ideally situated for? Designers whose vision extends beyond the 16:9 rectangle traditionally associated with video screens — with tickers, strips and vertical columns becoming common requests.
Neoti can leverage its broad LED experience, manufacturing panels to order that can be installed in almost any layout imaginable.
Before a single diode is soldered, however, it is vital that the manufacturer collaborate directly with design teams and integrators to fully understand a wide range of considerations, including what type of content will ultimately be displayed on the panels and how they will be mounted.
This is how Neoti prefers to work with broadcast clients — creating an ideal blend of expertise and creativity that only a team of manufacturers, integrators and scenic designers can provide. With this approach, broadcast clients using Neoti products can avoid costly errors that could lead to delays or a less-than-ideal end result.
It’s not all about price
Pricing is, of course, also a big concern for any broadcaster making the investment in LED.
Neoti admits upfront that it’s not willing to sacrifice quality for the sake of price — and so it won’t always be the lowest — but is equipped to engineer a wide range of solutions to fit a wide range of budgets.
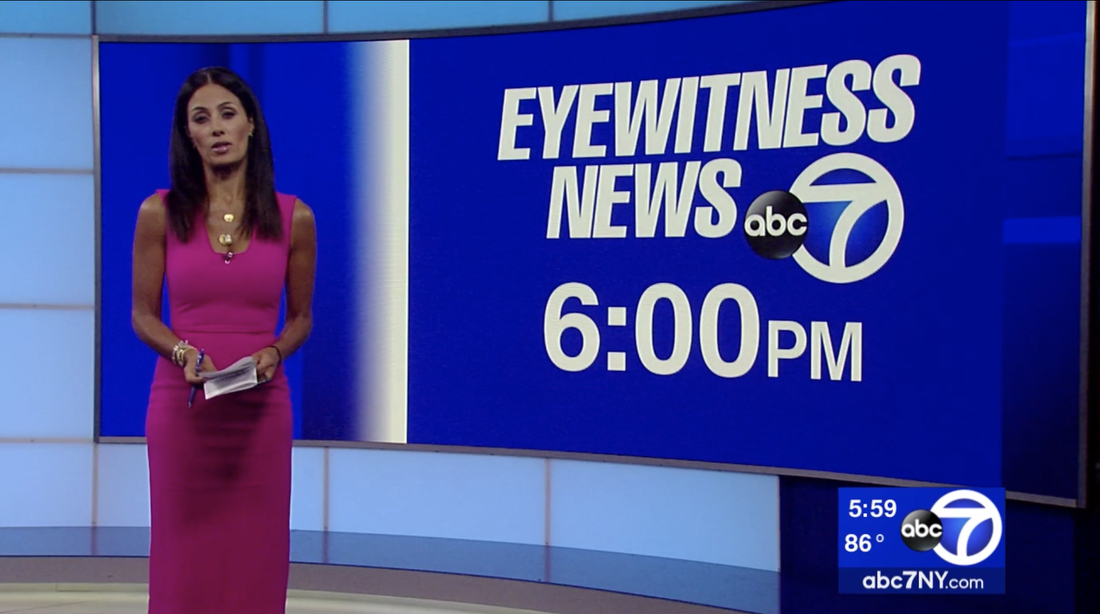
LED video wall from Neoti at WABC, which updated its previous LCD on-set technology with LEDs.
“Everything you put into an LED affects its price,” explained Kipfer, before listing an array of technical components that make up Neoti’s product line options.
The sheer number of options — and their potential effect on price, picture quality and longevity are all important factors to consider.
How component options affect not only price but the real-world use of the panel is a key portion of the wealth of knowledge and expertise Neoti brings to any project, integrator relationship, or client, notes Kipfer.
Metal matters
One of the biggest considerations is whether to use gold or copper bonding.
When diodes are manufactured, each surface mounted device, or SMD, that houses the red, green and blue diodes that work together to create a palette of millions of colors needs to be soldered so that the electrical signals that instruct the diodes how and when to light up can be passed along.
This is accomplished thanks to a hairline solder of copper or gold. Despite the minuscule amount used, the cost can quickly compound with projects that use upwards of hundreds of thousands or millions of SMDs.
Copper is, of course, less expensive than gold — typically around 20% less — but can lead to more issues over the long term.
“That information isn’t usually provided to the customer or buyer,” said Kipfer, a common pain point he sees when a customer is comparing prices.
“Many quotes out there are for substandard product,” noted Kipfer, adding that a “great deal” could end up needing significant repair or replacement after just a few years and ultimately end up costing more.
While most TV studios are fine using copper, since there typically aren’t swings in humidity, heat or exposure to elements, it is still worth noting that not every broadcaster has the budget to replace LED every few years. A larger upfront investment in gold bonding could be a better move if the panels need to last closer to 10 years.
No matter which bonding is used, all of Neoti’s panels are professional grade and designed to be left powered on 24 hours a day, 7 days a week — either in “standby” mode, simply being fed black or, in some cases, showing an image when not in active use.
Here again, Neoti can tailor specifications and provide estimated life cycles based on how and how often the video panels will be used, including providing expertise to graphic designers on how to create animated imagery that doesn’t put too much strain on a particular area of the panel.
As with any electronic device, each SMD is subject to failure rates and going with gold can reduce those. It’s important to note that, especially with higher resolution panels, most failures are not immediately noticeable, explained Kipfer.
When issues do pop up, however, Kipfer stresses the importance of having a manufacturer who supports its products.
Post-sale support
Neoti provides a wide range of post-purchase services and support, including replacing or repairing a wide range of components.
“Shopping by price can cause the biggest headache — what do you do when something’s not working?” said Kipfer, who explained that many, often less expensive, manufacturers have cut back on service and support hours due to the pandemic.
Neoti proudly maintained its staff during the pandemic and provides trained technicians to answer questions, troubleshoot issues and, if necessary, provide site visits.
“Our ability to provide critical support and service post-sale in very responsive ways is always a priority,” said Kipfer, adding that every member of his team goes through regular training each year.
Timelines
Project timelines are another area that can be a bit of a surprise for those new to the world of professional-grade LED panels, but this is also something Neoti provides guidance and updates on.
The process isn’t like buying a consumer-grade TV at your local electronics store, especially if your project has unique requirements that mean the panels aren’t kept in stock in a warehouse.
Typically it’s best to buy all the panels from the same batch to use on one project, so this generally requires them to be made on-demand. This can take anywhere from 30 to 45 days for the project to be manufactured and pass quality checks.

LED video wall at the ACC Network from Neoti.
Customers should also consider shipping time from Neoti’s overseas plants. Not surprisingly, that’s been heavily affected by the COVID-19 pandemic, but even under normal circumstances this still requires some patience to be done right and cost-effectively.
All told, Neoti advises planning ahead, even outside of a global pandemic, and allowing at least four to six months to complete the consultation, manufacturing, delivery and installation processes.
Looking ahead
Looking toward the future, Neoti is hard at work looking at customer needs from 2020 to enhance its products and services during 2021, reflecting its responsive approach to the market and dedication to existing product lines.
This already includes UHD products, and the company is also constantly exploring ways to deliver lower costs and better value to customers.
While the company closely monitors emerging technologies such as mini and micro-LED, flip chip, GOB and more, its goal is to be “leading edge” rather than “bleeding edge” so that it can deliver cost-effective products that the market is ready to accept and install.
“A lot of these new products are great,” said Kipfer, ”but we’re focused on creating products that actually serve a purpose – not just look good on the show floor.”
Learn more about Neoti and download a free case study on UHD LED for broadcast studios on its website.
The above column is sponsor-generated content from Neoti. To learn more about sponsor-generated content, click here.
Subscribe to NCS for the latest news, project case studies and product announcements in broadcast technology, creative design and engineering delivered to your inbox.
tags
LED, LED Displays, LED Tiles, LED Video Walls, LED walls, Neoti, Video Walls
categories
Partner Content